Lab Services
Our team comprises skilled chemists, metallurgists, and laboratory technicians. As a comprehensive laboratory service provider, we conduct analyses and testing adhering to international standards. Moreover, our team can be dispatched for on-site analyses when required. With a particular focus on Metallurgy Analysis, we assist in uncovering critical insights into the structure and properties of metal and alloy samples.
Interconnect Analysis (for ICs)
Package Disassembly and Analysis
Interfacial Structure and Bonding Analysis
Quantitative Elemental Analysis and Spatial Mapping
Microstructural Characterization and Phase Quantification
Evaluation of Grain Structure and Grain Size Distribution using SEM and Image Analysis
Identification and Characterization of Failure Interfaces
Micro-hardness Characterization of Materials and Layers
Surface Roughness Measurement and Analysis
Comprehensive Metallurgical Testing Services
Physical Analysis
Optical Microscopy
Scanning Electron Microscopy (SEM) for high-resolution imaging assets
Scanning Transmission Electron Microscopy (STEM) for advanced materials characterization design
Field-Emission Scanning Electron Microscopy (FESEM) for high-resolution imaging downtime
Transmission Electron Microscopy (TEM) for high-resolution imaging and crystallographic analysis
Atomic Force Microscopy (AFM) for surface topography and mechanical property measurements
Particle Size Analysis (PSA) for determining particle size distribution
Electron Backscatter Diffraction (EBSD) for crystallographic orientation mapping
Surface Profilometry for surface roughness measurements
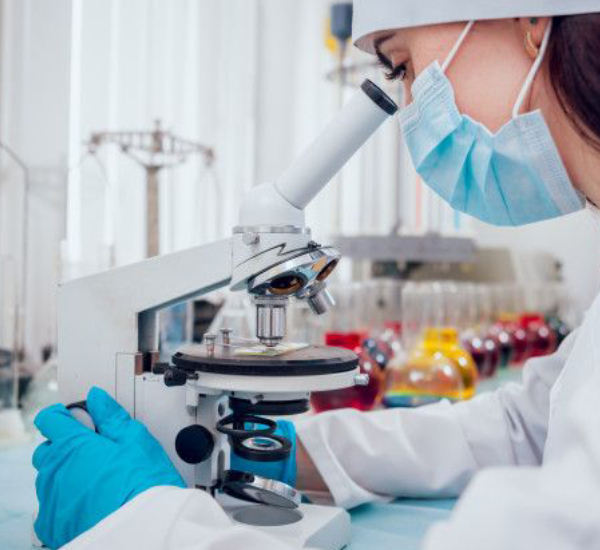
Material Analysis
-
Energy Dispersive X-Ray Spectroscopy/Mapping (EDS): Non-destructive elemental analysis using X-ray emission.
-
Fourier Transform Infrared Spectroscopy (FTIR): Identification of functional groups based on characteristic vibrational frequencies.
-
UV-Visible Spectroscopy (UV-VIS): Measurement of electronic transitions in the ultraviolet and visible regions.
-
Photoluminescence Spectroscopy (PL): Analysis of radiative recombination processes in materials.
-
Thermogravimetric Analysis (TGA): Measurement of mass change due to processes like decomposition, dehydration, or absorption.
-
X-Ray Fluorescence (XRF): Elemental analysis based on X-ray fluorescence phenomena
-
X-Ray Photoelectron Spectroscopy (XPS): Measurement of electron binding energies for surface elemental and chemical state analysis.
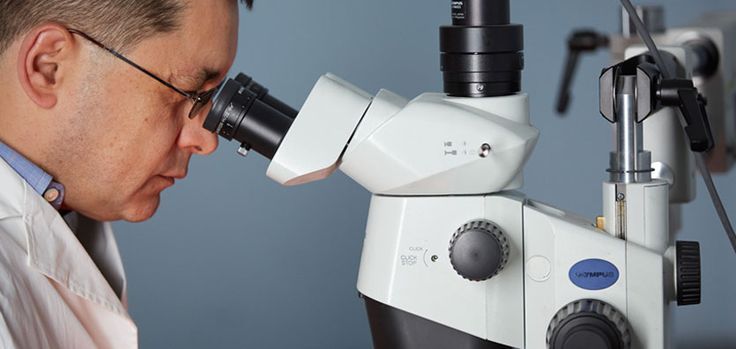
-
Differential Scanning Calorimetry (DSC): Measurement of heat flow associated with phase transitions, melting, or crystallization.
-
Auger Electron Spectroscopy (AES): Analysis of Auger electrons emitted from atoms for elemental identification.
-
Time-of-Flight Secondary Ion Mass Spectrometry (TOF-SIMS): High-sensitivity surface analysis based on time-of-flight mass spectrometry of secondary ions.
-
Electron Energy Loss Spectroscopy (EELS): Measurement of energy loss of electrons interacting with a sample for compositional and electronic structure analysis.
Chemical Analysis
-
Ion Chromatography (IC): Separation of ions based on their affinity for an ion-exchange resin.
-
Inductively Coupled Plasma Optical Emission Spectroscopy (ICP-OES): Elemental analysis based on the emission of light by excited atoms in an inductively coupled plasma.
-
Inductively Coupled Plasma Mass Spectrometry (ICP-MS): Highly sensitive elemental analysis based on the mass-to-charge ratio of ions generated in an inductively coupled plasma.
-
Gas Chromatography-Mass Spectrometry (GC-MS): Separation of volatile compounds by gas chromatography followed by mass spectrometric identification.
-
Atomic Absorption Spectroscopy (AAS): Measurement of the absorption of specific wavelengths of light by atoms in the ground state.
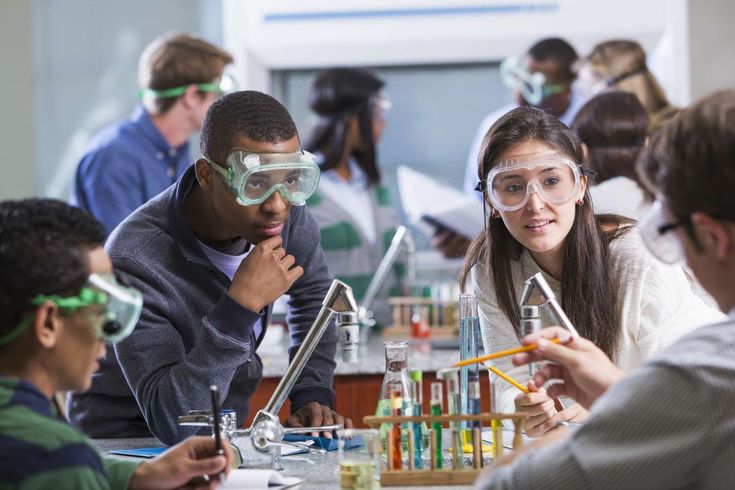
-
Volatile Organic Compounds (VOCs): Organic compounds with high vapor pressures at room temperature.
-
Optical Emission Spectroscopy (OES/Arc Spark): Elemental analysis of solid materials using the emission spectra generated by an arc or spark discharge.
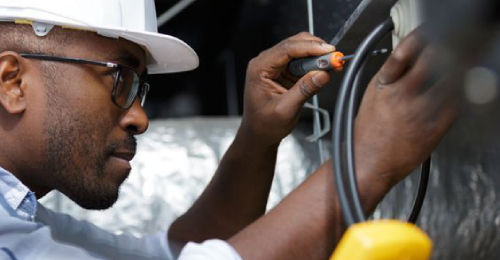
Mechanical Test
Brinell Hardness Test
Rockwell Hardness Test
Microvicker Hardness Test
Bend Test
Tensile Test
Charpy Impact Test
Metallurgical Analysis
Metallurgical analysis employs a range of techniques to reveal the microscopic structure of materials. By examining this microstructure and its patterns, we gain insights into the material's processing and manufacturing conditions, which are key to optimizing its production. Additionally, this analysis helps determine if the product adheres to the necessary standards and specifications for its intended application
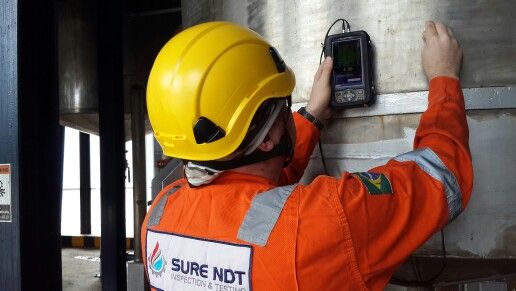

Sample Preparation
While various analysis techniques receive considerable attention, the importance of sample preparation is sometimes overlooked. However, obtaining the desired images and results critically depends on proper sample preparation methodology. Furthermore, the skill and experience of the laboratory personnel performing this preparation are not just essential, they are absolutely crucial.
Non-Destructive Test
-
Dye Penetrant Crack Test: Widely used in various industries, including aerospace, automotive, and manufacturing, to inspect components for cracks, porosity, and other surface defects.
-
Magnetic Particle Crack Test: Commonly used in the aerospace, automotive, and power generation industries to inspect welds, castings, and forgings for cracks and other defects.
-
In-situ Metallography: Used to assess the effects of corrosion, fatigue, and other factors on the microstructure of materials in critical components, such as aircraft engines and nuclear power plant components.
-
In-situ Hardness Test: Used to assess the hardness of materials in critical components, such as aircraft engines and nuclear power plant components, to ensure they meet design specifications and can withstand the expected loads.
-
Nondestructive testing (NDT): It is a crucial initial step in failure analysis, allowing investigators to determine the cause of failure without damaging the sample or the evidence.
-
NDT is commonly applied throughout a component's lifespan, including during service, to identify conditions resulting from wear, fatigue, corrosion, stress, or other factors that can impact reliability.
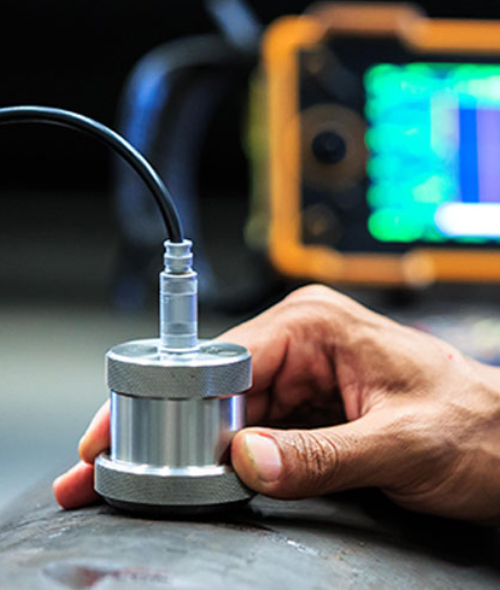